Nabeaquam
BoTM Winner
It follows the fork curve.I think woz we're all bumbling novices when presented with the wizadry of Nabeaquams bike!
It's from another century but almost like from another planet! Well to me it is
I can see it being brazed by a wizard yep... doable.....it's cutting that join.....I just can't my head round the neatness and consistency of it by hand! But to tool up a machine to cut that in steel would be so expensive I just can't see the cost effectiveness for such low volume! If it was cut by a machine they're would definitely have to be other applications for that kind of tubing...
Nabeaquam.....is the joint stitch on the forks a straight line or does it follow the curvature of the fork?
I have a late 1920s Gloria. It has Italian high quality tubing made under a German patent. It was also bent and worn out, but not as bad as this current project. I have a set of reamers, threaders and facers for bicycles. I tried to fix it myself but the steel was so brittle that I made a mess. I sent it to a frame maker and he couldn’t fix it as it was brittle. He replaced two tubes and the drops. He removed dents, did a track alignment and spread the drops from 114 to 120 mm. He thought it might have been furnace brazed but because of the steel brittleness I’m now thinking it may have been brazed with a blowtorch. The net info indicates that a blowtorch had a wide flame. Interesting. Here is the Gloria tubing stamp. I can’t find much about this tubing.
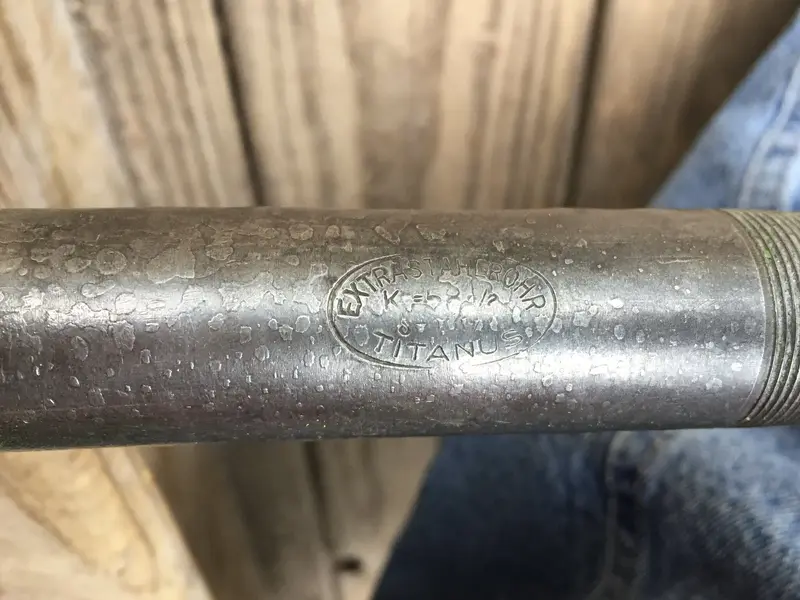