vcballbat
Senior Retro Guru
Not exactly sure when Ian Phillips took over the helm as Raleigh's Chairman and Managing Director from Tom Barnsley .. maybe 76-77... this film is dated December 1977. What I do know is that Ian Phillips resigned as Chairman and Managing Director on the 28th July 1981 as confirmed in this document from Raleigh.
https://www.macearchive.org/films/atv-today-13121977-raleigh-cycles-factory
https://www.macearchive.org/films/atv-today-13121977-raleigh-cycles-factory
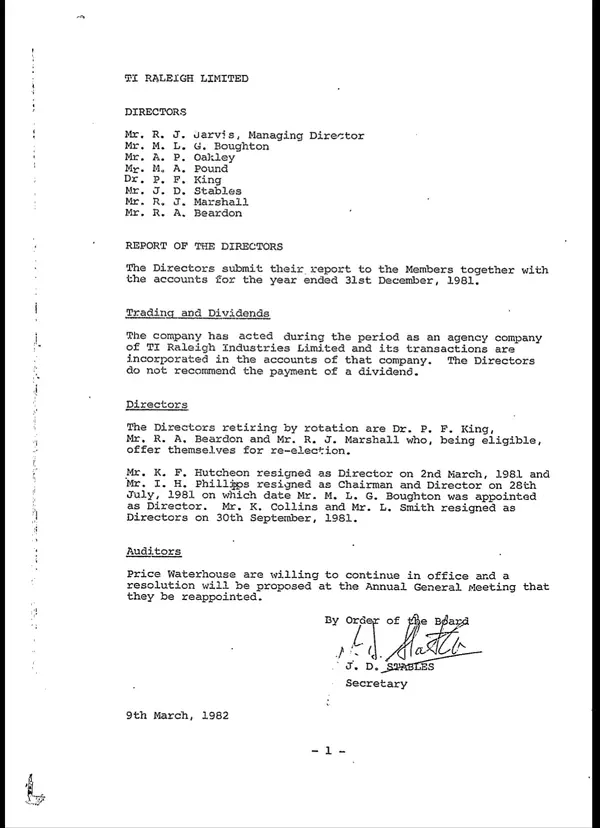