MuchAlohaNui
Senior Retro Guru
Good stuff, thank you for the link! Worst case if there is a problem finding the right diameter, I may consider nylon or teflon bushings and trim/drill to size.Unfortunately I can´t help you much with any of your questions/problems, but rest assured that I´m eagerly following your journey.
Only for the bushing problem you may find a solution here:
https://www.igus.de/iglidur/zylindrisches-gleitlager
Thanks man! I am pretty sure these are all original hardware. Some of those cranks have three different anodization processes and three different colors. Worth a try. Worst case I strip off the mistakes and anodize a solid color to the crank arms.Good stuff Brandon. Kooka Racha levers never had titanium bolts or parts originally, although it’s plausible that your set have been retrofitted with aftermarket bits over the years.
So will you be graduating onto and experimenting with more advanced Kooka colours?
Star12
View attachment 750019
I think at this point in time with my fourth attempt of anodizing the brake lever parts (a blue this time). As you (all) can see in the photo here, the blue is very muted, very dull. Me thinks the anodization time needs to be reduced OR the anodization bath is too contaminated to move forward OR I am pushing too many volts through the parts. Does the blue look "dull" or "opaque" to you (or anyone else)? Ahhh! Or, this finish is considered "patchy" which may be due to fluctuating voltage during the anodization bath. Man...titanium is so much easier...
Edit: I am also thinking too with all my anodizing lately that the chemicals in the foam from these Rachas have leached out and mixed with my solution compounding the unstable and problematic state if the anodization adhering to the metal surface. Thinking out loud primarily here too. I need to add this to my thread to maybe help out the next guy who tries to do similar stuff in his kitchen

Anywho, do you happen to know where to find similar foam grips to these old Kooka's? I am tempted to cut them off completely and put on something similar and new if possible.
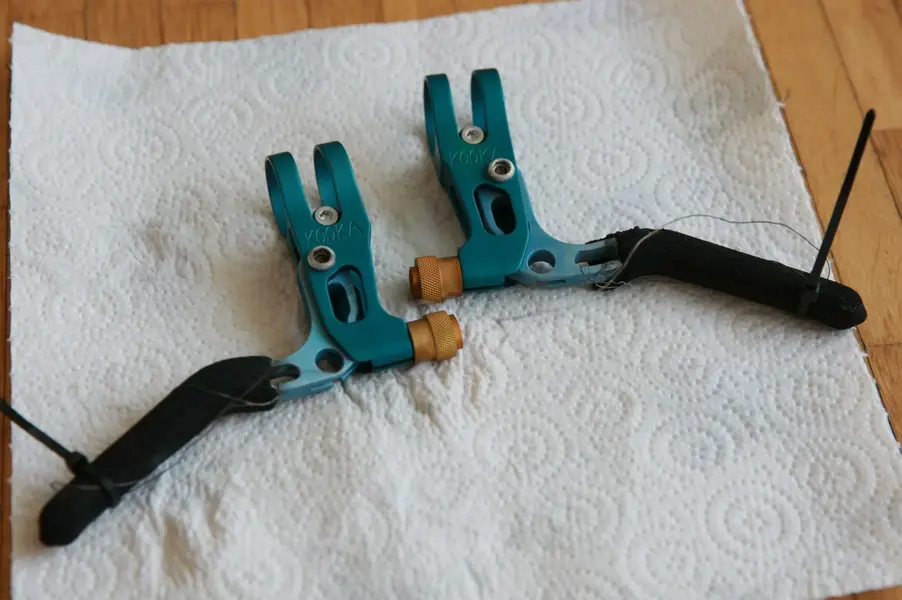
Last edited: