LumPi Panda
Retro Guru
- Feedback
- View
A short section of 1mm square styrene strip fits into each slot...
...then the treads slide onto the rod. Using square rod helps to keep all of the treads lined up nicely.
Once the big bit is stuck on, the two tiny little triangles can be superglued onto the other tyre half to complete the classic Z-Max Z
The central row of Z treads is made of 416 individual bits, plus countless others that end up flying out of the tweezers into oblivion
I think they used a similar exercise in Guantanamo bay.
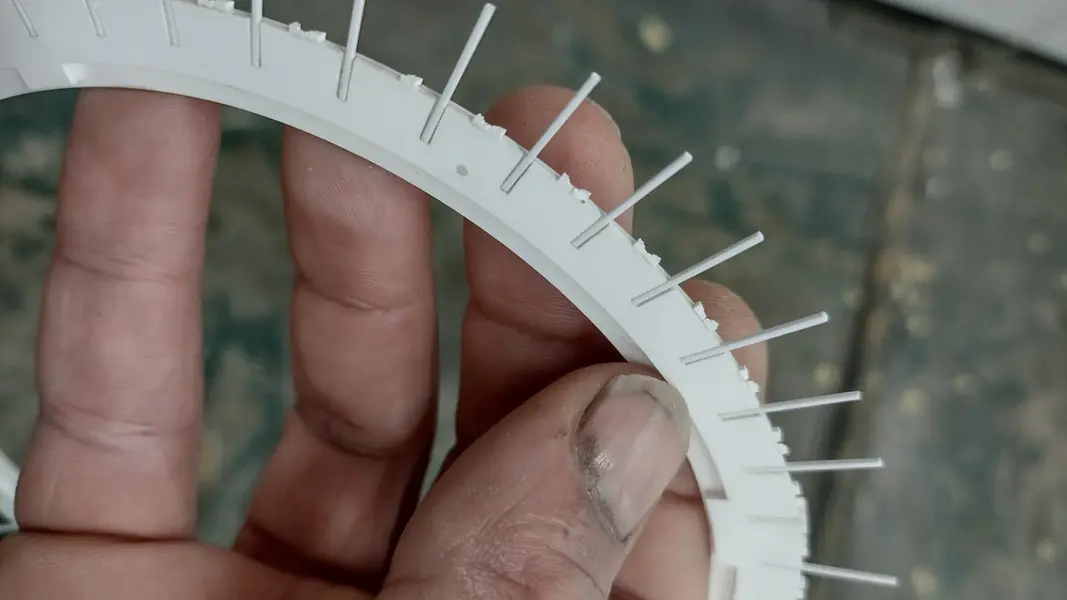
...then the treads slide onto the rod. Using square rod helps to keep all of the treads lined up nicely.
Once the big bit is stuck on, the two tiny little triangles can be superglued onto the other tyre half to complete the classic Z-Max Z
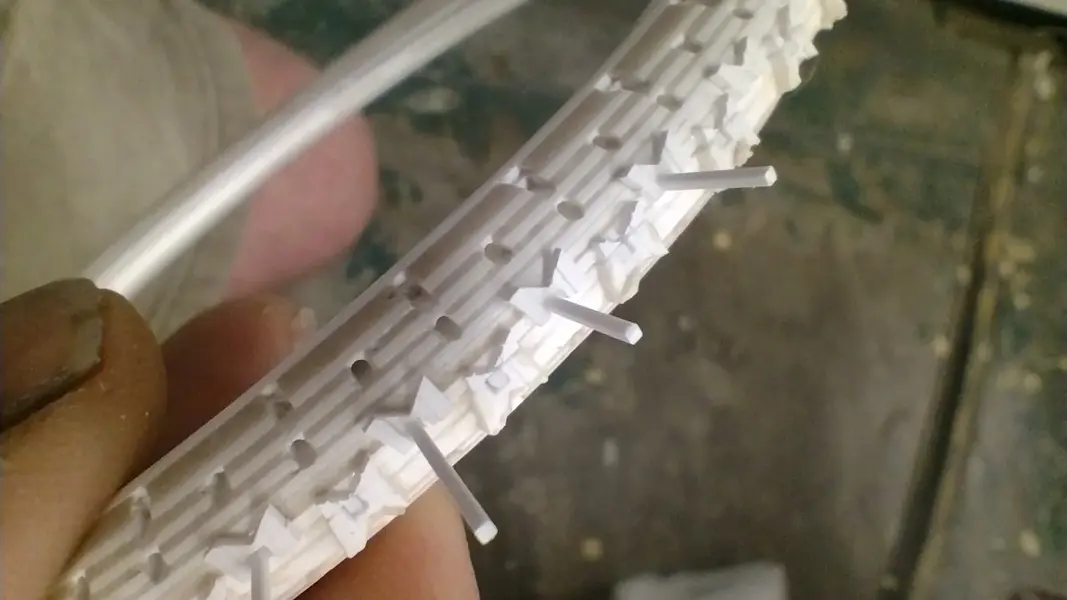
The central row of Z treads is made of 416 individual bits, plus countless others that end up flying out of the tweezers into oblivion
I think they used a similar exercise in Guantanamo bay.
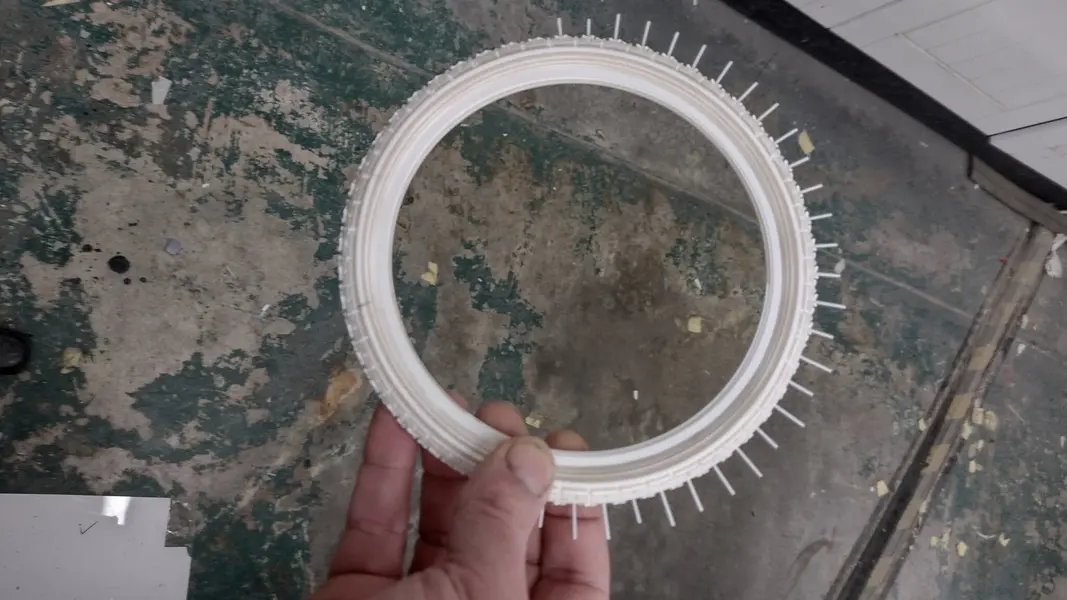