Nabeaquam
BoTM Winner
Putting 7/8 brake levers on one inch bars isn’t easy. I wanted to do it without welding extensions on the brake lever clamps. I got the clamp as close as I could by bending and squeezing and then pounded in a Phillips head screwdriver to align the clamp ends as best I could.
A lot more forcing is required.
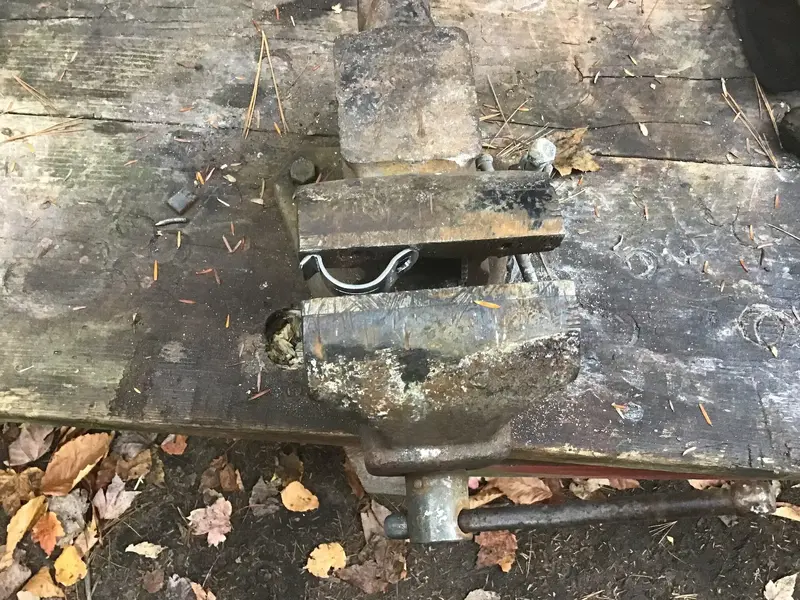
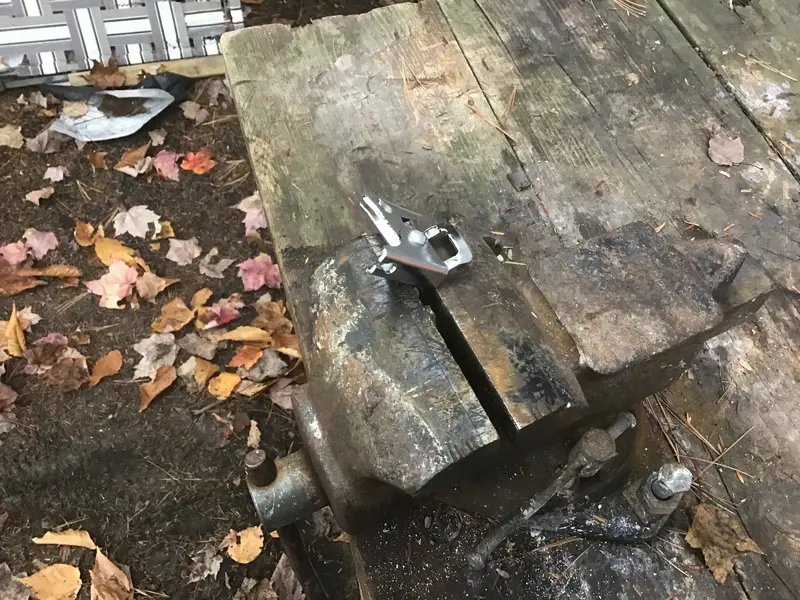

A lot more forcing is required.
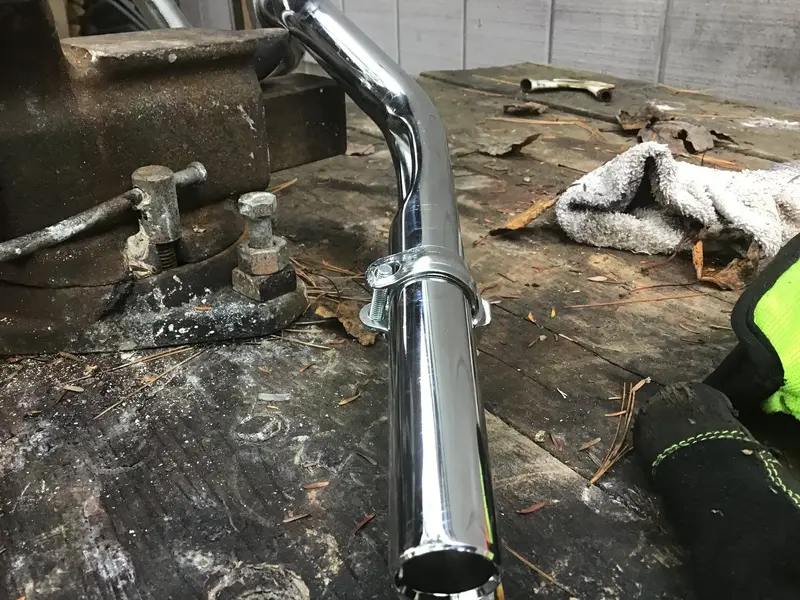
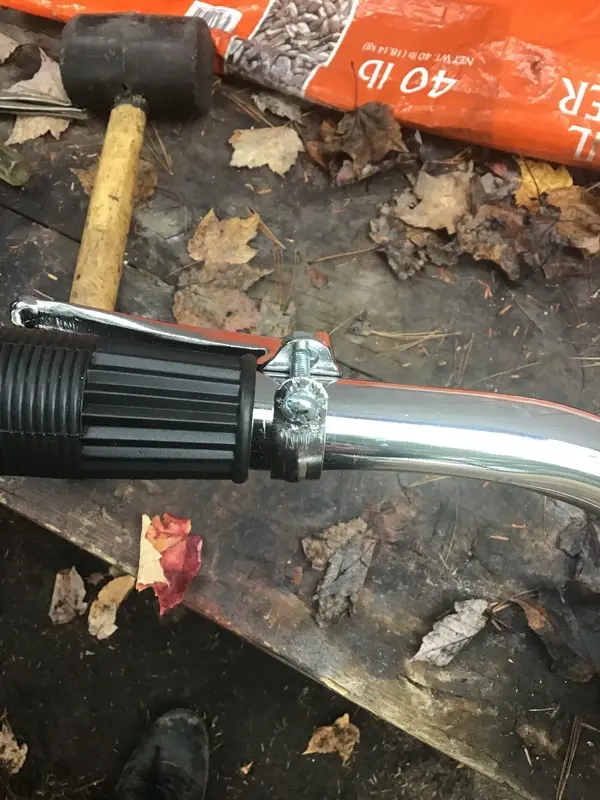
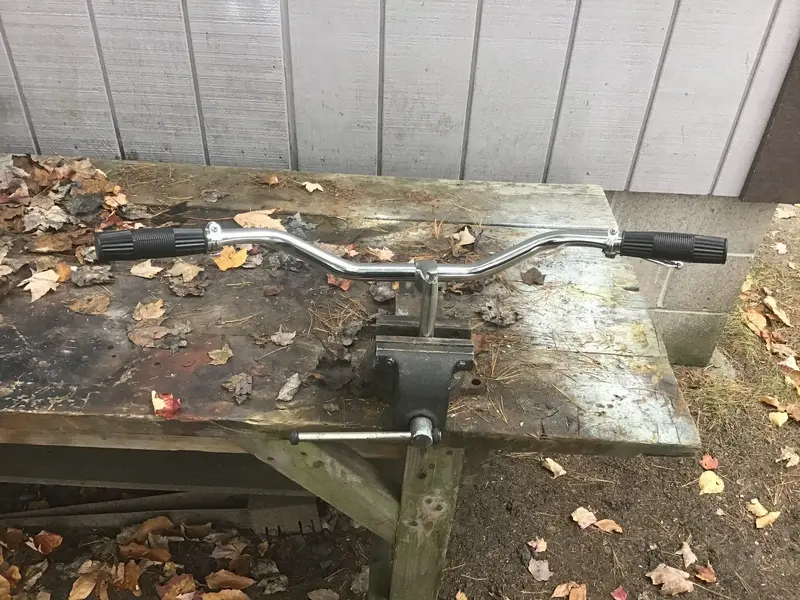
Last edited: