This stuff can be done...don't scrap your frame or hang it on the wall.
Here's the problem:
Someone fitted a 26.8mm seatpost instead of a 27.0. The post could then rock inside the seat tube, stressing the weld and cracking around the collar:
So, I hacksaw along the remaining weld, along the crack line down to the original tube surface, and lifted off the clamp piece:
Strip the anodising with a strong caustic soda solution and a non-organic paintbrush...the Pace stuff is very tough, it takes some time, light abrasion to cut the anodising and plenty of refreshes of the solution.
Here you can see the different reaction of the 7005 body material and the 5356 weld material to the caustic soda. The black is some of the non-aluminium alloying components which aren't dissolved being precipitated on the surface.
Quick dip into a nitric acid de-smut solution to clean the precipitate off.
Machine and file off any remnants of the original weld and put a chamfer on the joint to make sure that the penetration is better than the original:
Same chemical strip of the top section of the seat tube:
Wash, light going over with silicon carbide abrasive cloth (not aluminium oxide, which can contaminate the weld), and finally an acetone degreasing wipe over. Leave to dry, then line everything up with an expanding bronze heatsink inside to reduce any distortion and tack up:
Complete the weld, running from least to most stressed areas. Finished:
The new weldment and surrounding original material will naturally age back close to 7005 T6 without an artificial ageing heat treatment cycle after around 30 days at room temperature.
Good for another 30 years.
All the best
Here's the problem:
Someone fitted a 26.8mm seatpost instead of a 27.0. The post could then rock inside the seat tube, stressing the weld and cracking around the collar:
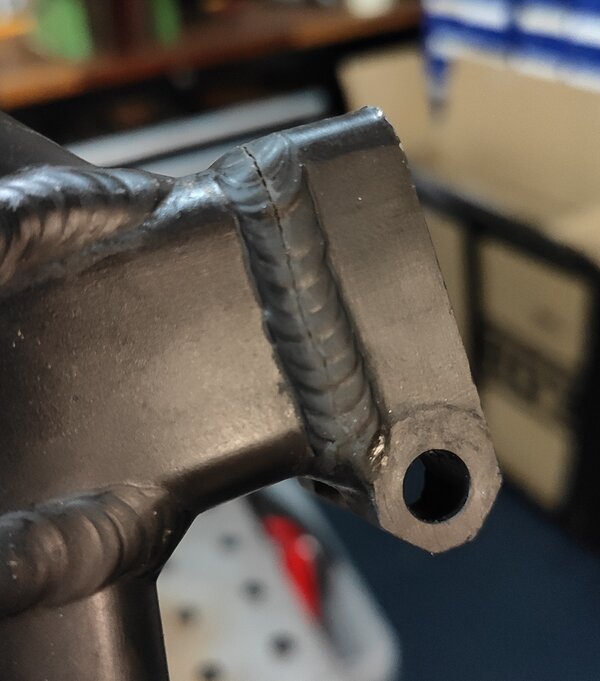
So, I hacksaw along the remaining weld, along the crack line down to the original tube surface, and lifted off the clamp piece:
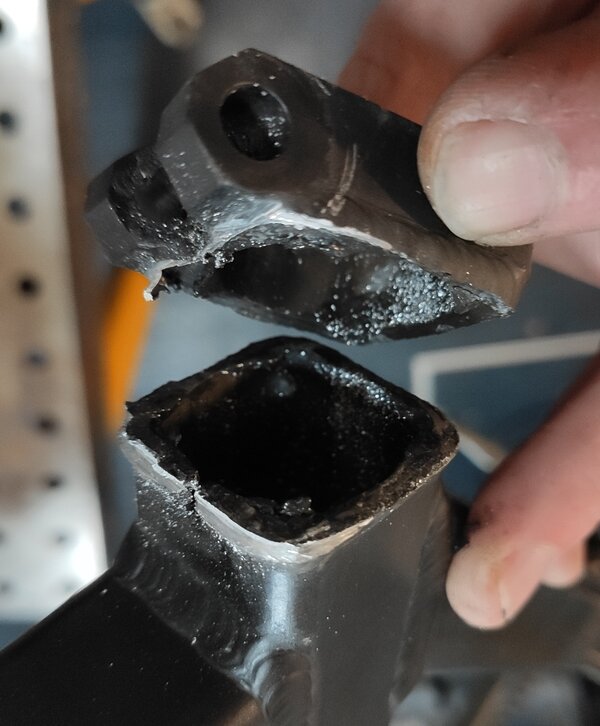
Strip the anodising with a strong caustic soda solution and a non-organic paintbrush...the Pace stuff is very tough, it takes some time, light abrasion to cut the anodising and plenty of refreshes of the solution.
Here you can see the different reaction of the 7005 body material and the 5356 weld material to the caustic soda. The black is some of the non-aluminium alloying components which aren't dissolved being precipitated on the surface.
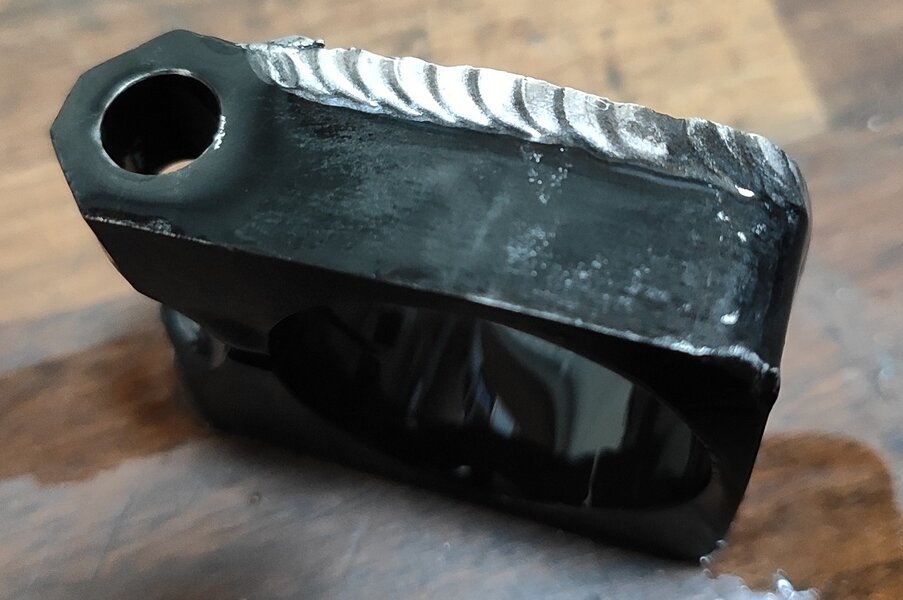
Quick dip into a nitric acid de-smut solution to clean the precipitate off.
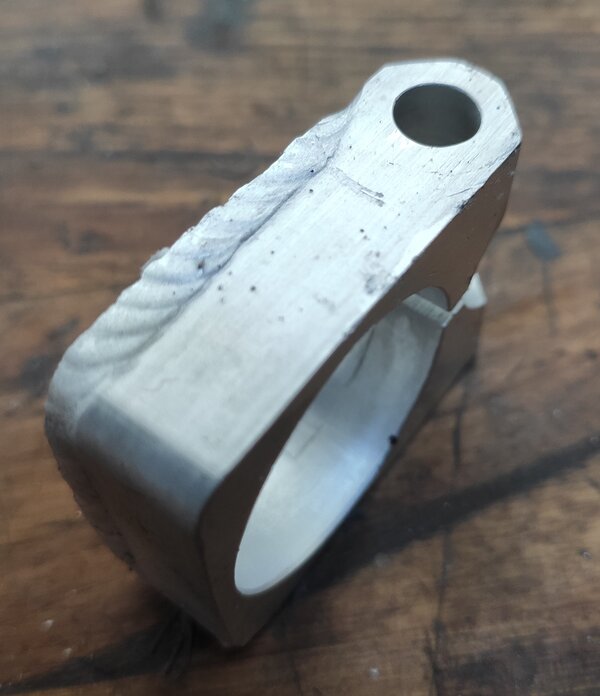
Machine and file off any remnants of the original weld and put a chamfer on the joint to make sure that the penetration is better than the original:
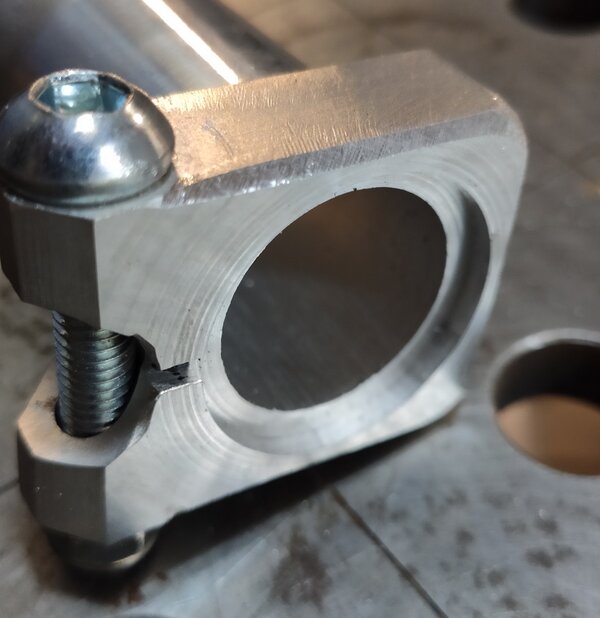
Same chemical strip of the top section of the seat tube:
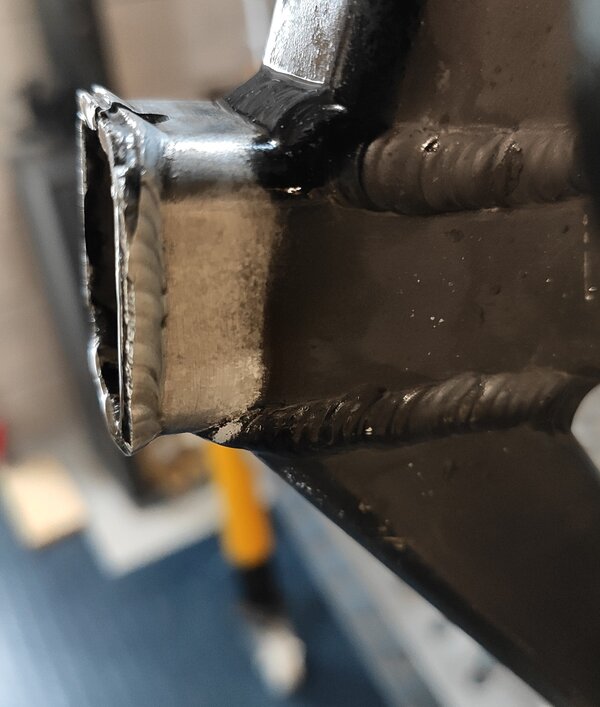
Wash, light going over with silicon carbide abrasive cloth (not aluminium oxide, which can contaminate the weld), and finally an acetone degreasing wipe over. Leave to dry, then line everything up with an expanding bronze heatsink inside to reduce any distortion and tack up:
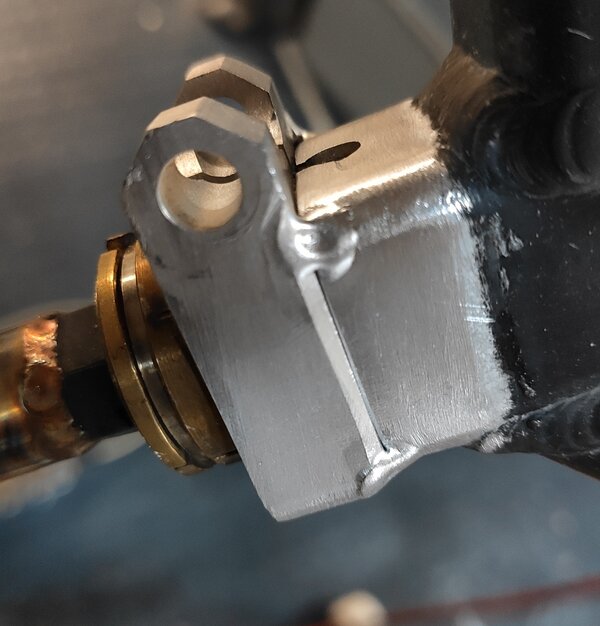
Complete the weld, running from least to most stressed areas. Finished:
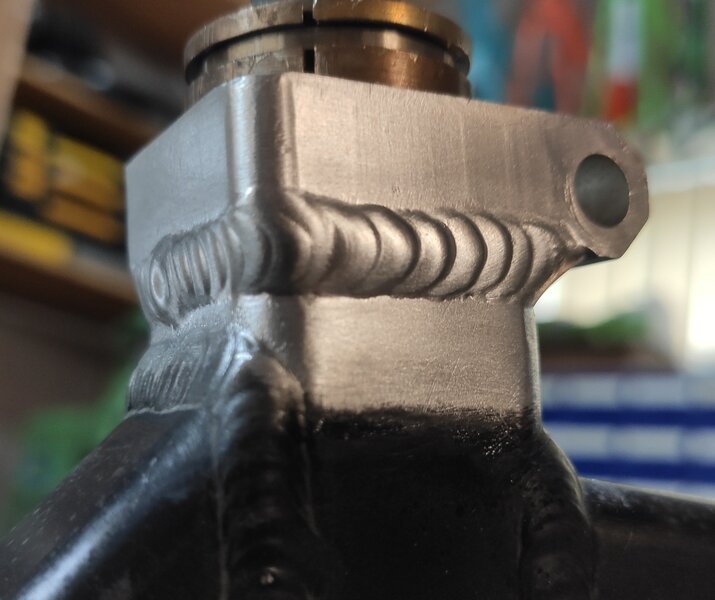
The new weldment and surrounding original material will naturally age back close to 7005 T6 without an artificial ageing heat treatment cycle after around 30 days at room temperature.
Good for another 30 years.
All the best