I couldn't resist a lovely (but unsold and silly cheap) Dawes Edge from @Gaddmeister
It required a canti stud repair. Repair kits are available (typically the Problem Solvers kit) but were going to struggle with the problem on my frame. A canti bolt had seized in the frame, and subsequent attempts to drill it out appeared to have failed. I bought the frame with a mangled stud. The problem was worsened by the boss being very close to the seatstay and a bolt could not be fitted through from the back.
Firstly the stud was sawn off the boss and the remains of the old canti bolt removed.
The stud would be replaced by one from a scrapped frame (in this case a Univega Alu-800 which had cracked).
The threaded bottom of the stud was removed to leave just the part for the canti and a tiny bit to allow a spanner to grip.
The boss was cleaned up and tapped with the correct M6 thread. A stainless M6 bolt was then driven through and into an M6 stainless Nyloc on the other side. Note the extra nut, more later!
The bolt was then withdrawn, with threadlock on it, back until tight.
The head of the bolt was then sawn off giving 8 threads for the stud to screw onto. Removing the nut cleaned the threads up allowing the stud to fit neatly.
The stud was tightened onto the thread, and secured with a little thread lock.
It required a canti stud repair. Repair kits are available (typically the Problem Solvers kit) but were going to struggle with the problem on my frame. A canti bolt had seized in the frame, and subsequent attempts to drill it out appeared to have failed. I bought the frame with a mangled stud. The problem was worsened by the boss being very close to the seatstay and a bolt could not be fitted through from the back.
Firstly the stud was sawn off the boss and the remains of the old canti bolt removed.

The stud would be replaced by one from a scrapped frame (in this case a Univega Alu-800 which had cracked).

The threaded bottom of the stud was removed to leave just the part for the canti and a tiny bit to allow a spanner to grip.
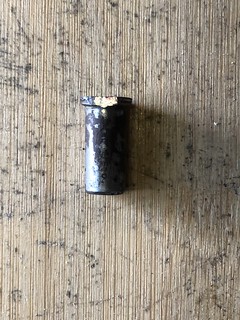
The boss was cleaned up and tapped with the correct M6 thread. A stainless M6 bolt was then driven through and into an M6 stainless Nyloc on the other side. Note the extra nut, more later!


The bolt was then withdrawn, with threadlock on it, back until tight.

The head of the bolt was then sawn off giving 8 threads for the stud to screw onto. Removing the nut cleaned the threads up allowing the stud to fit neatly.
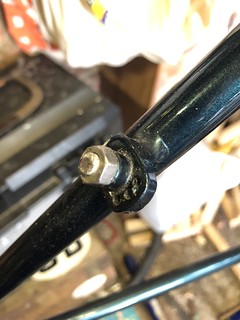
The stud was tightened onto the thread, and secured with a little thread lock.

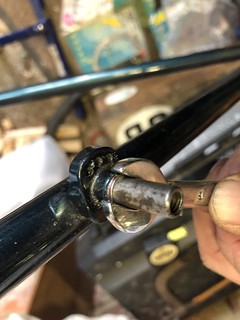
Last edited: